Curing a greener concrete: Minnesota tests roads paved with carbon-injected concrete
Drivers on Interstate 94 west by Albertville are part of an experiment to lock up carbon pollution in concrete.
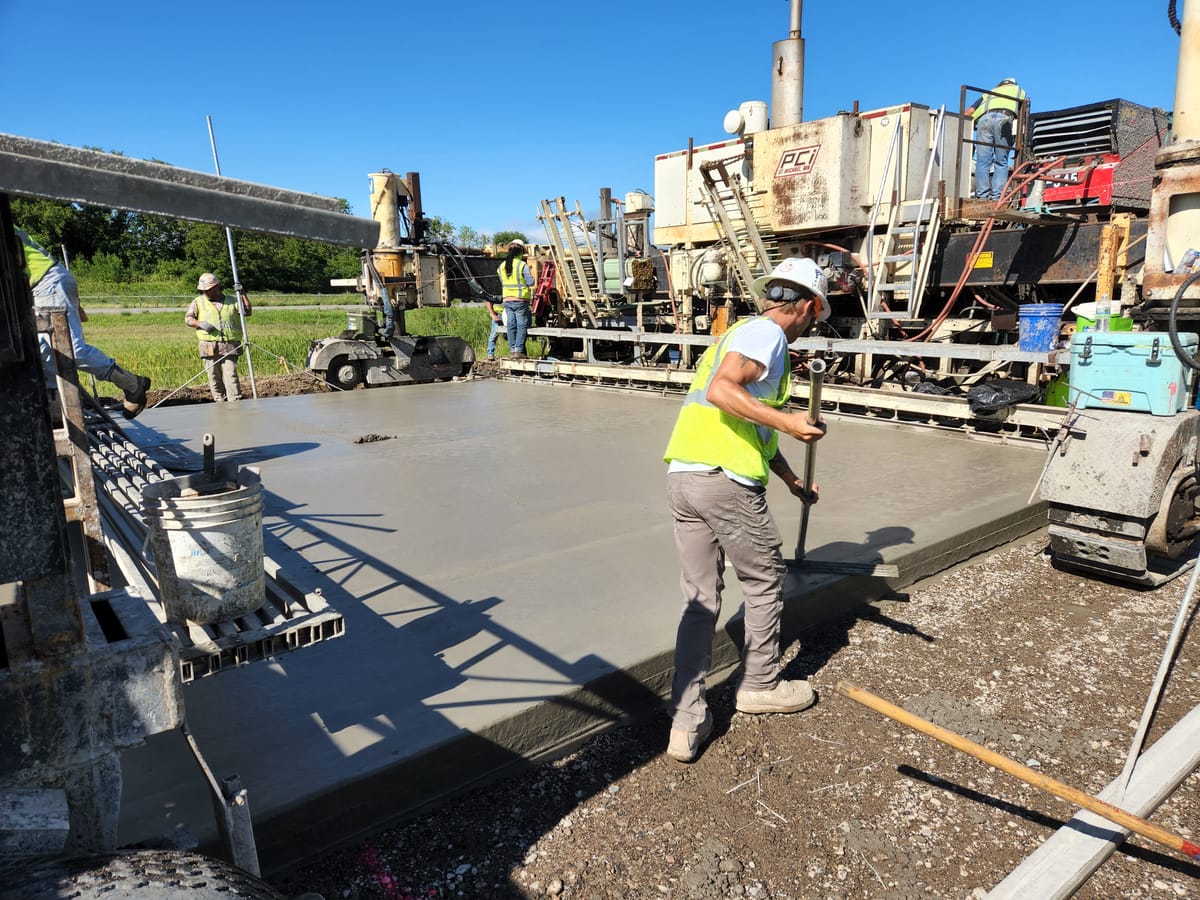
Minnesota’s future roadways could one day have a lower carbon footprint.
Researchers with the Minnesota Department of Transportation, in cooperation with 13 agency partners, are studying how to capture and store carbon dioxide in concrete, a process called sequestration. The result could reduce the carbon footprint of concrete, if successful.
Concrete is used to construct roads, bridges, foundations, buildings, walls, wastewater and stormwater systems, sidewalks, and more. It’s the most widely used material made by humans at 25-30 billion metric tons annually, said Dr. Halil Ceylan, co-principal investigator on the project and a professor at Iowa State University.
“These are wonderful steps to improve our sustainability, especially environmental sustainability by sequestering carbon dioxide — given the gigantic amounts of concrete that we use, second only to water,” Dr. Ceylan said. “And let’s say we sequester 1% (of carbon dioxide) by weight: that will be a very significant amount.”
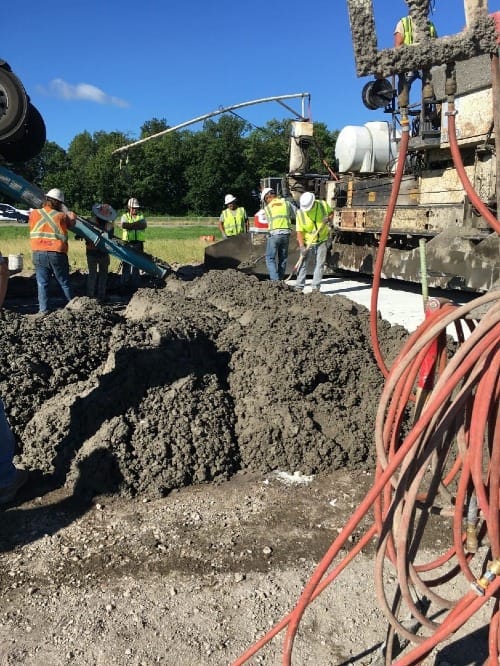
The transportation industry is prioritizing sustainability, said Dr. Bernard Izevbekhai, research operations engineer with MnDOT and the project’s technical liaison. Because of that, officials have been looking for ways to make concrete more sustainable without sacrificing strength, durability, and versatility.
The experiment is testing two technologies — CarbonCure and Carbon Upcycling — that claim to reduce the amount of carbon dioxide used during the production of concrete while also improving the concrete’s performance, said Dr. Peter Taylor, principal investigator on the project and a professor and director of the CP Tech Center at Iowa State University.
Test slabs of concrete using the products are being compared to regular, MnDOT-grade concrete. Both products sequester carbon dioxide when concrete is being made, which requires less cement during the production process.
“With less cement in the system, we reduce the carbon footprint,” Dr. Taylor said. “By binding up the CO2 in the system, that carbon dioxide's removed from being free in the atmosphere.”
The research contract is $150,000 from the National Road Research Alliance pooled fund with Iowa State University, according to Ben Worel, executive director of NRRA and an operations engineer at MnROAD.
The experiment
Test slabs were poured at MnDOT’s MnROAD facility near Albertville in 2022. The project will run through 2025, with researchers testing the concrete in a variety of ways.
The team looks at as many data points as they can, from how easy to construct the product is, to how the pavement handles load, how the load transfers between joints, what the ride feels like, and more, said Dr. Izevbekhai.
When Project Optimist spoke to the researchers in January, they were still combing through their first year of data.
“Suffice it to say that we haven't seen any terrible performance,” Dr. Izevbekhai said.
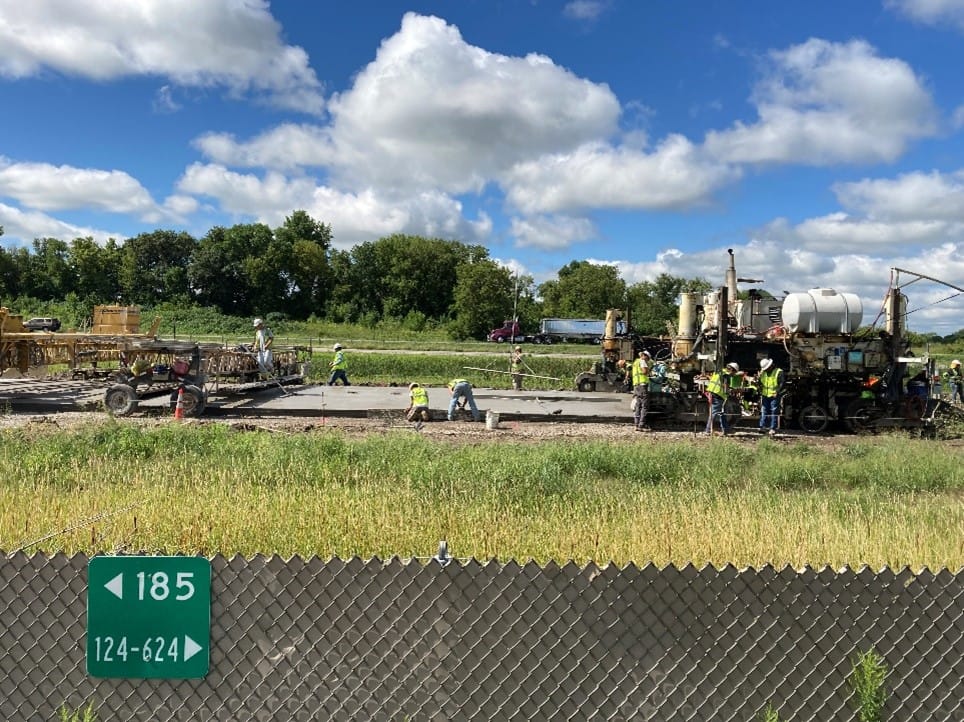
So far, the researchers have run into a few roadblocks. One came when the test slabs were poured. The ready mix plant was a 40-minute drive from the MnROAD facility, which Dr. Taylor said slowed down the concrete delivery. As a result, the paving machine wasn’t able to keep moving during the process.
“What I suspect – and this was true not only of the sections we were watching under this project, but almost all of them – is that the paver would sit for maybe 20-30 minutes with a load of concrete underneath it that hadn't yet been fully leveled, consolidated, smoothed, finished,” he said. “And so by the time it came out of the back of the paver, it was starting to set, and so the smoothness and the texture were not ideal.”
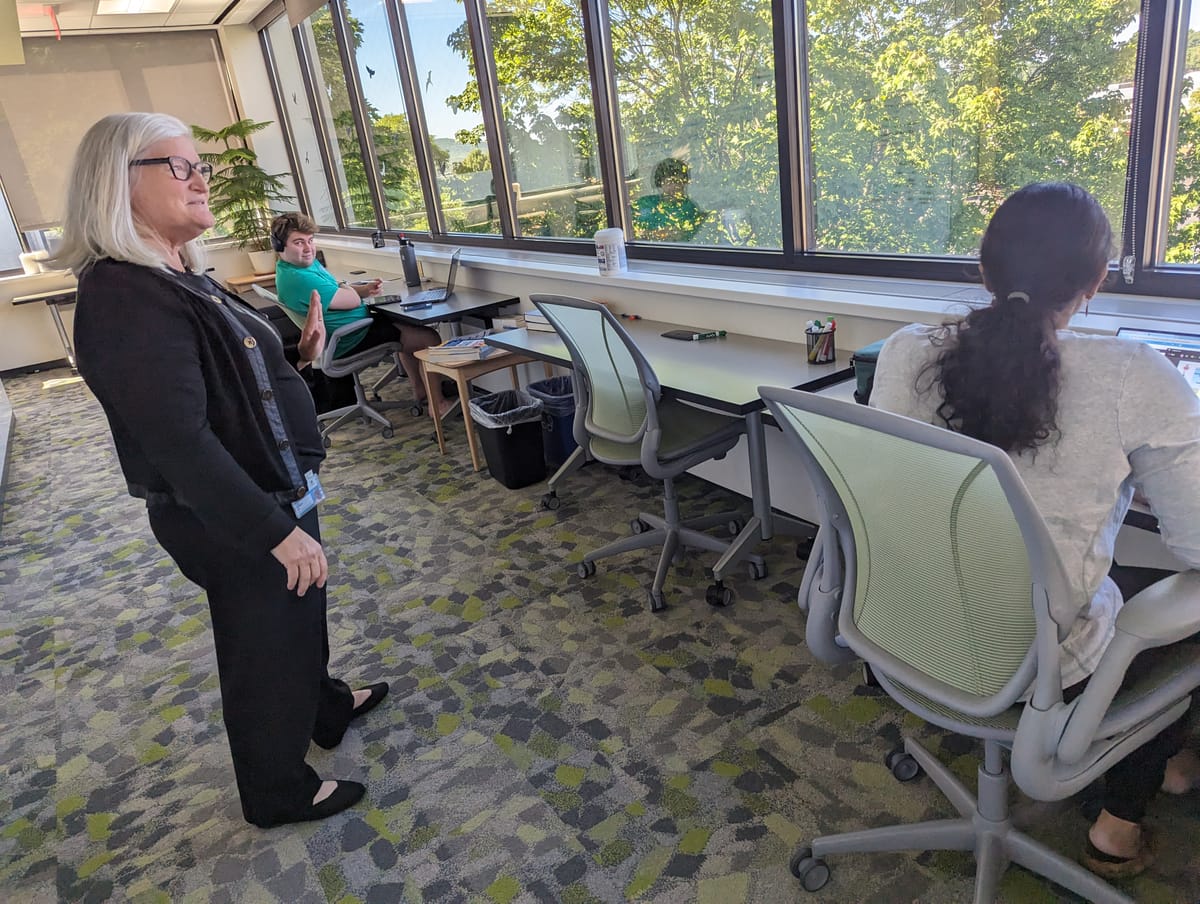
As a result, the researchers had to use a diamond grinder on the pavement to get the texture they wanted, Dr. Izevbekhai said.
Another issue is that officials from CarbonCure said they didn’t remove as much cement from the mixture as they could have for their test sections, Dr. Taylor said. Attempts to reach CarbonCure for comment were not successful.
The team would have liked to see a similar amount of cement removed in Minnesota as the company has done in places like Hawaii, Dr. Izevbekhai said.
“We are seeing differences that are not as significant as we had seen in other prior usages outside of Minnesota. So to us, that's quite a challenge, and it makes us determined to use a very, very rigorous tooth comb to look at other performance indices, like load transfer efficiency … ride, we want to look at those very closely,” he said.
Defining success
The team is also figuring out how to calculate the amount of carbon dioxide sequestered during the production process, which has proven challenging thus far. The researchers are working with colleagues at the National Institute of Standards and Technology in Gaithersburg, Md., Dr. Taylor said.
“Thus far they haven't been able to find a good test method to detect the CO2 to the precision that we need to get a signal. So whether or not that'll ever happen, I'm getting kind of cynical, but we keep hoping that they'll be able to do it,” he said.
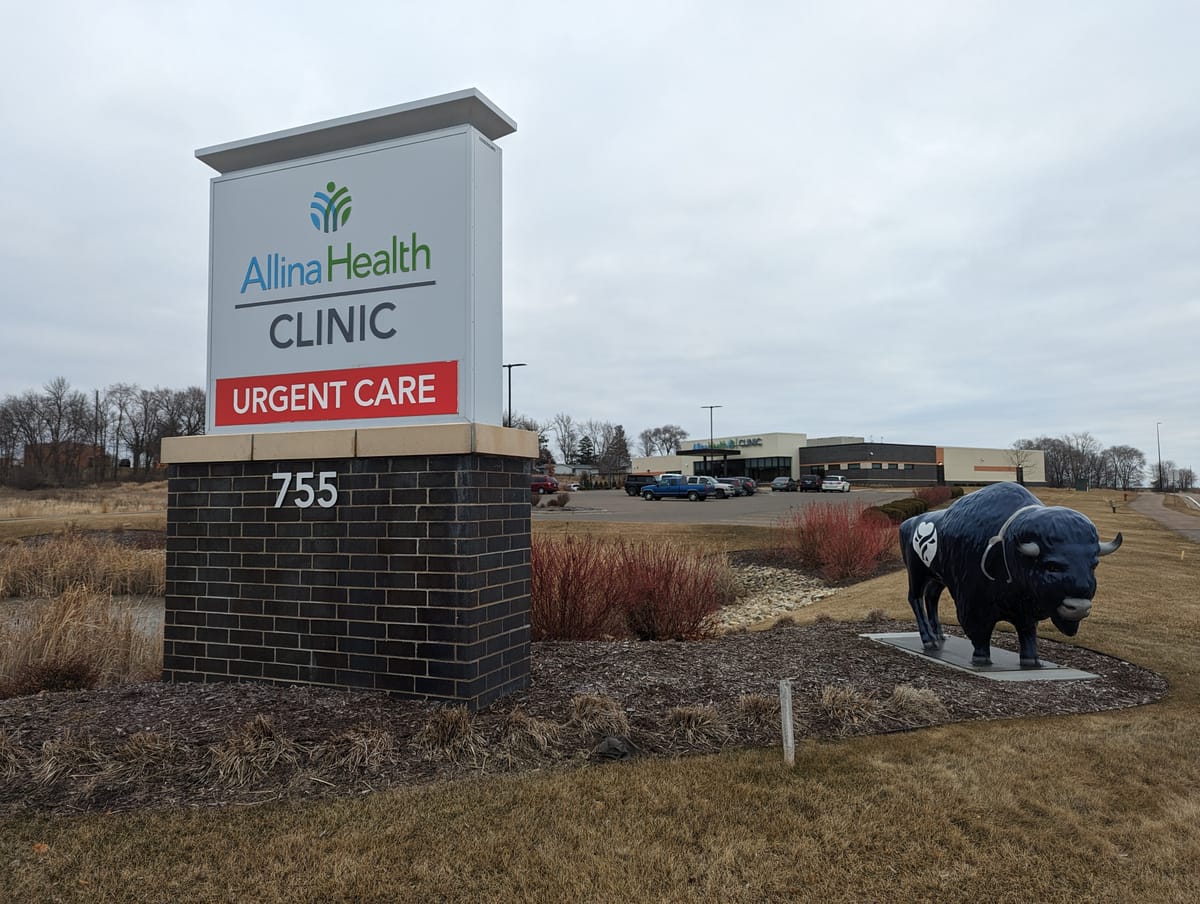
When asked what their definition of success is for the project, Dr. Taylor distinguished between the project and the product.
“Success of the project is collecting the data and being able to make sense of it,” he said. “Success of the product would be reducing carbon footprint.”
There is widespread interest in reducing the carbon footprint related to infrastructure. Dr. Izevbekhai said that was clear during the Transportation Research Board’s 2024 conference in Washington, D.C., which was held in January.
“Sustainability is not just a cliche, it’s actually a goal,” he said.
Cement vs. concrete - what’s the difference?
Concrete is made from several materials, including cement.
Cement is a powder that when mixed with water creates a paste. Construction workers can then add different things to cement to create different materials. For example, adding sand to the paste creates mortar. Mixing the paste, mortar, and stones up to an inch in diameter creates concrete.
This story was edited by Nora Hertel and Becca Most. It was fact-checked by Nora Hertel.